Steel industry built to last
Global steel markets go from strength to strength, as investors look for a new safe haven
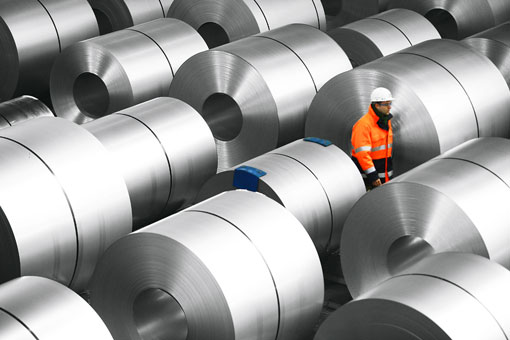
In the giant plants of Hebei Iron and Steel group, the biggest steel-maker in China, no less than 130,000 employees are at work. Established in 2008 through the merger of three companies in the Hebei province, the state-owned company with total assets of 190bn yuan [$30bn] is the second-largest in the world and a symbol of the nation’s voracious appetite for its output.
With 45 percent of the world’s steel pouring out of its factories, China has become the undisputed catalyst of a global industry in overdrive in practically every region except the EU. “China remains the steam engine of the global steel industry,” points out Ernst & Young industry specialist Peter Markey.
If China is firing on all cylinders, so is India. Already the fifth-biggest producer, it is forecast to leapfrog three places to take the number two spot within the next few years. At 54kg per head, current consumption is low by the standards of emerging markets but several elements have gone into the pot to change that.
In short order, central and regional governments have worked to eliminate some of the murky approval processes that created investment bottlenecks, encouraging more international investment. Around $1trn is due to be pumped into steel production in India over the next two or three years to satisfy the voracious maw of construction, infrastructure and automotive industries. The first two alone account for over 60 percent of consumption.
The financial crisis certainly didn’t slow South Korea. The sixth-biggest producer, it exploited the situation to reduce costs so dramatically that its two giants, POSCO and Hyundai Steel, are able to undercut long-time rival Japan by 36 percent on international markets. Indeed China is a major buyer from South Korea.
But that’s just in Asia. Blessed by ample supplies of coking coal, ore and scrap, blast furnaces are running 24 hours a day in Russia, the world’s fourth-biggest producer. They’re being fired by a government that feeds contracts and roubles to steel-intensive industries – automotive, machine-building, oil and gas, and manufacturing. Russia is also one of the biggest exporters of steel, with almost half of production being sold abroad by companies such as Severstal, Novolipetsk and Evraz.
One of the clouds on the steel-making horizon is a global shortage of raw materials such as coking coal, a vital element in production, and iron ore. According to steel analysts, there is no immediate likelihood of the dearth in coking coal being resolved, but this is a highly innovative industry and much work is being done on ways of reducing or even eliminating the use of coking coal in the production process.
Another looming problem is security and cost of supply. Inevitably, the rapid increase in growth in production has pushed up prices for all raw materials involved in the manufacture of steel and there has been a frantic scramble to protect reliable and affordable commodities through a variety of arrangements such as exclusive contracts and joint ventures.
The more innovative companies such as Nucor, one of the largest US producers that claims to recycle a tonne of steel every two seconds, responded to the rising cost of materials by developing higher grades of steel that attract higher prices.
The financial crisis only served to slow global production, but not everywhere and only briefly. It had grown at a merry seven percent a year to hit 1.327bn tonnes by 2008, but production plunged by 36 percent in the US and by 31 percent in the EU. Then driven by the booming economies of the big three – China, India and Brazil, production was back to 1.4bn tonnes by 2010. In fact the insatiable appetite for steel in China hardly abated with demand rising by 15 percent even in the middle of the financial crisis.
The distribution of steel is undergoing what could be a revolution to match in scale and significance what has happened in technology in the last few years.
Brazil’s industry, already boasting some of the best steel-making technology, is in the forefront of a sea-change that aims to control as much of the supply chain as possible. Having assured a ready supply of raw materials and low-cost production by gaining control of mines and energy producers, Brazil’s market-leading companies are now moving into logistics so they can distribute steel right up to their customers’ factories in just-in-time deliveries. The country’s fast-growing automobile industry is a direct beneficiary.
Some Brazilian producers are taking distribution a step or two further by establishing mills as satellite production units that add value to the raw steel, directly meeting customer requirements.
For the rest of 2012, industry observers such as Eurometals, the UK-based international trading firm, expect the industry to maintain what looks like more or less unstoppable growth. Although demand for steel may cool somewhat in China, its forecasts reveal that it’s rising in Japan as it recovers from the Fukushima disaster, in USA and in Brazil.
Meanwhile China is flexing its muscles in other ways. In late January it launched its first physical iron ore trading platform in a partnership with China Beijing International Mining Exchange and the powerful China Chamber of Commerce. Ominously for foreign competitors, Hebei Iron and Steel and other major producers immediately signed up.
To vote on The New Economy 2012 Steel Industry Awards, click here.