Plasco Energy Group’s advanced technologies turn waste into an opportunity
Plasco Energy Group’s Executive Vice President of Operations explains how the company’s advanced conversion technology will efficiently convert waste to energy and fuels, revolutionising waste management

Plasco’s demonstration facility, Plasco Trail Road. The company has developed advanced technologies that convert waste into energy and fuels
There is a growing global realisation that the increasing quantity of municipal solid waste (MSW) produced each year constitutes not only a challenge but also a significant opportunity. The energy content of MSW is high – ranging from 9,000 megajoules (MJ) per tonne at the lower end, up to 16,000MJ at the higher end for prepared RDF. If this energy is captured efficiently and in an environmentally friendly manner, the need for landfills would be significantly reduced, while also allowing for the substantial generation of renewable power. By 2022, the projected 2.9 billion tonnes of global MSW could provide approximately one million GWh of electricity per year: enough to power nearly 300 million households.
Realising this goal requires advanced technologies that combine innovations in thermal conversion, and chemical and environmental engineering into processes that are tailored for the optimal transformation of waste into energy. There are many significant technological challenges that must be overcome to successfully develop a process that can achieve high efficiency, low emissions and near total transformation of waste into energy.
Plasco Energy Group, based in Canada, has invested over CAD400m, and built on research efforts that began in the mid-1970s, to develop an advanced thermal conversion technology that can make this vision a reality. The Plasco Conversion System (PCS) is an advanced plasma-assisted gasification process that efficiently converts up to 95 percent of post-recycled MSW into high-quality syngas and other co-products, with emissions of dioxins and furans that are below the limit of quantification. The syngas can be used to power internal combustion engines for energy generation, or as a chemical feedstock for further refinement into transportation biofuels or other applications.
Advanced conversion technology
The path to developing an advanced waste-to-energy technology is lengthy and requires a significant investment of capital to test and refine the process at a near commercial scale. The development of the PCS began in 1974, when Plasco’s predecessor RCL Plasma partnered with various industry leaders to explore the use of plasma for the destruction of hazardous waste. RCL began applying plasma gasification to waste remediation in the 1980s and commissioned a five tonnes per day pilot plant to support ongoing R&D. Subsequent collaboration with the National Research Council of Canada helped to further develop and validate the concept.
1m
Potential GWh produced from MSW by 2022
300m
Potential number of households powered by MSW by 2022
In the late 1990s, RCL partnered with one of the largest waste managers in Spain (Hera Holding) to move the pilot plant to Spain for continuous process improvement and refinement. This R&D led to the achievement of proof of concept of a plasma-assisted gasification process in 2006, in which plasma was only used where it had the greatest impact on producing a clean syngas, rather than simply applying plasma directly to the MSW for gasification. The upgraded pilot plant was used to refine the design and operational parameters for a larger pilot facility that was closer to a commercial scale.
Plasco was founded in 2005 after the amalgamation of RCL and its majority-owned sister company, Plasco Energy Corporation. It commissioned an 85 tonnes per day pilot facility at the City of Ottawa’s Trail Road landfill site in 2008. From 2008 to 2011, Plasco designed and tested the core unit operations of the PCS in separate purpose-built vessels with positive results. Extensive technology development revealed that separating the key stages of conversion (gasification, melting and refining) enabled each stage to take place in customised vessels tailored to their unique requirements.
In order to reduce mechanical complexity, improve process efficiency and reduce the footprint of the plant, Plasco combined all core unit operations into an Integrated Conversion and Refining System (ICARS), which was installed in 2011. From 2012 to date, technology development work has been focused on final process optimisation, and cost reductions driven by an iterative process in collaboration with Black & Veatch (a global leading engineering consulting, construction and operations company). Black & Veatch conducted a technical review of the demonstration technology, and in 2014 concluded that the technology was ready for commercialisation.
Plasco’s process gasifies waste in a low-oxygen and low-temperature environment using only recycled process heat, and then refines the resulting syngas and vitrifies solid residue through the optimised application of plasma. Gasification does not combust waste, but rather heats the feedstock with a controlled amount of oxygen. Plasco’s system requires significantly less syngas cleaning and conditioning than other technologies because the low-oxygen environment prevents the formation of dioxins and furans and reduces the total volume of gas to be processed.
The syngas is used to fuel high-efficiency internal combustion engines. A steam turbine generator is powered by exhaust heat from the engines and recycled process heat for combined cycle power generation. A deliberately small unit capacity that can convert 200 tonnes per day (scalable to match community requirements), results in a minimal plant footprint and enables local waste management and power generation. Low emissions and the absence of a tall industrial smokestack both streamline public approval » and environmental permitting processes. The cost and emissions associated with transportation to large regional treatment centres is eliminated by Plasco’s distributed solution, which also realises lower energy losses by generating electricity inside power grids.
Process efficiency
Process efficiency is the key driver of both the financial and environmental benefits of a waste-to-energy conversion technology. Generating significant net electricity per tonne of MSW leads to improved financial returns, and also increases the reductions of greenhouse gas emissions realised by displacing power generated from fossil fuels.
There are a number of unique features of the PCS that contribute to class-leading efficiency. First, the process separates and customises chambers for each stage of conversion, optimising the environment for each stage. Second, proprietary equipment maintains ultra-low process oxygen levels, enabling gasification (and subsequent plasma refining) to take place at low temperatures, which in turn lowers process energy requirement. This unique approach enables the entire primary gasification of waste to be powered only by recycled process heat. Third, an ultra-low oxygen environment also minimises the development of highly toxic compounds, which reduces the energy required for downstream syngas conditioning.
Plasco made a strategic design choice to use plasma for refining and melting solid residue rather than for the primary gasification of waste. This targeted approach of using plasma to refine the syngas focuses plasma where its active species can crack long-chain hydrocarbons, rather than using it directly to provide heat to gasify waste.
Unlike other plasma gasification processes, which heat waste directly with plasma (a highly inefficient heat source), the PCS does not require the addition of coke or other fuels to the MSW to be economically viable. The need for syngas conditioning is further reduced because Plasco positioned the Gas Quality Control Suite prior to combustion, reducing the volume of gas to be cleaned.
These innovations enable the PCS to generate more net energy per tonne of MSW than other thermal processes.
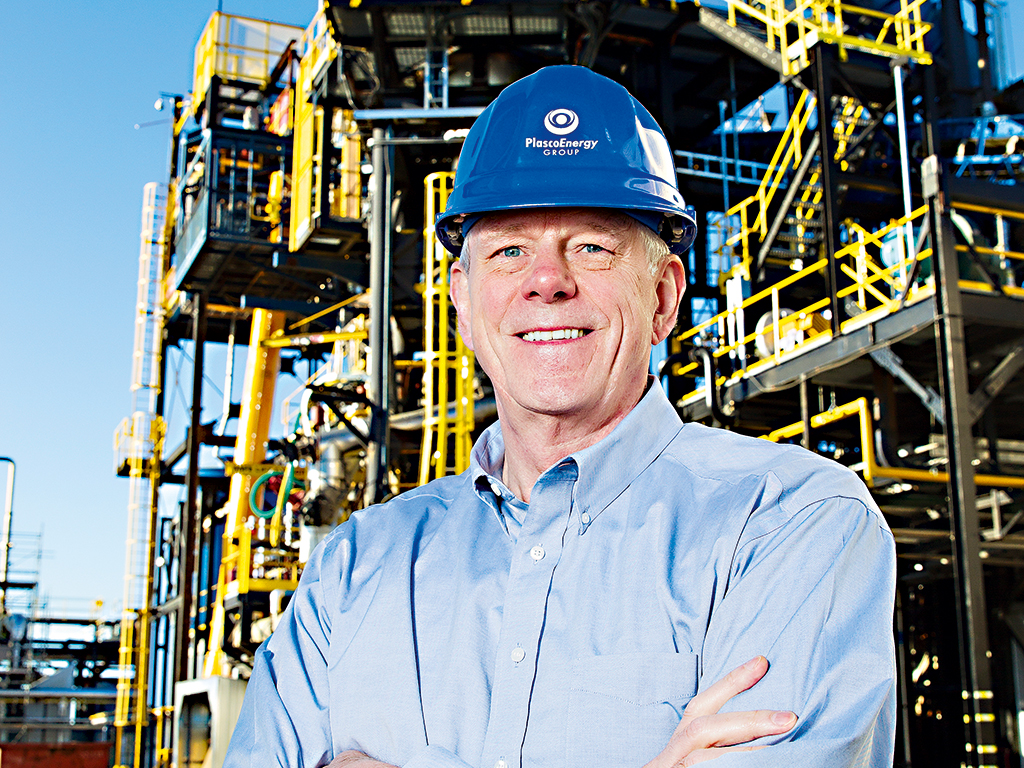
Environment and feedstock
Low emissions, high efficiency and the ability to divert up to 95 percent of waste from landfills are the primary drivers of the environmental benefits of Plasco’s conversion technology. The Ottawa PCS reduces the generation of CO2 equivalents by 924kg per MWh of net energy generated. These reductions are realised by diverting waste from landfills, which generate greenhouse gases through the release of methane during the decomposition of waste.
Scheduled to begin operation in 2017, Plasco’s first commercial plant in Ottawa, Canada will reduce emissions of CO2e by 67,400 tonnes per annum.
One of the challenges to emerging advanced waste-to-energy technologies is that many require municipalities to implement costly waste sorting facilities to provide the highly controlled feedstock that they require. Plasco’s proprietary control system ensures high-quality syngas is consistently produced, even from a constantly changing waste stream. The technology offers unique feedstock flexibility, with the ability to process a wide variety and mixture of carbon-based waste streams, including black bag municipal waste and higher energy refuse-derived fuels, without any pre-processing required by municipalities.
Where water usage is an issue, plants can be configured for dry cooling, reclaiming water in the waste to a quality suitable for surface discharge or industrial applications. Alternately, plants can be designed for wet cooling with zero liquid discharge.
Plasco’s future
Ray Floyd recently joined Plasco Energy Group as President and CEO, bringing more than 30 years of experience with energy industry leaders Exxon Mobil and Suncor Energy. Floyd has led some of the world’s largest and most complex energy operations, and has an international reputation as a thought leader in Operational Excellence. Floyd says: “What attracted me to Plasco was the opportunity to work in a different part of the industry that I had not previously experienced. This became even more compelling given the quality of our key investor group, including ARES Management, Quantum Group (George Soros) and successful Canadian investor WestFace Capital, who are positioned to support an innovative disruptive technology platform.”
Plasco is continuously working to improve its technology by utilising the latest developments in plasma technology and related fields. Plasco’s team is developing an optimised method of refining syngas, which would further reduce the temperature of the process, improving overall efficiency. Plasco is also increasing the automation of several features of the process to further reduce the labour required. Both of these developments will be implemented at the Ottawa commercial facility.
Floyd says: “There is an overwhelming global need for a clean and economic solution to the issue of municipal waste management, and answering that global need is Plasco’s mission.”